Hydrogels rapidly switch from soft to hard to create smart medical bandage
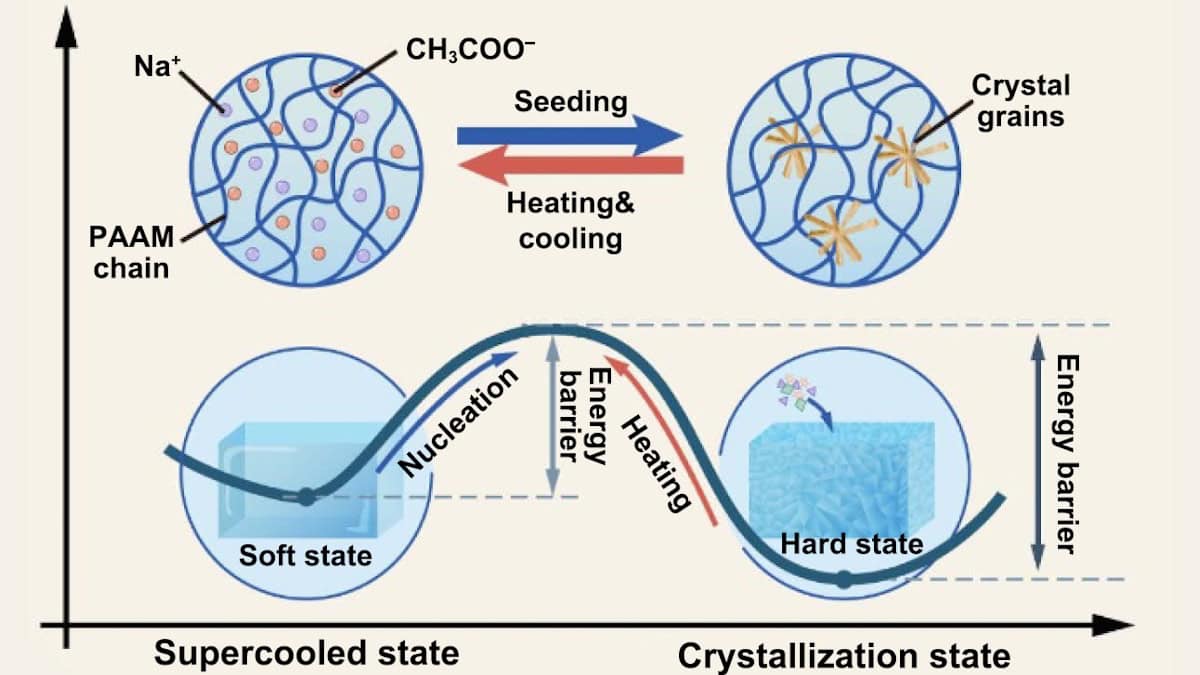
Complex hydrogel structures created using 3D printing are increasingly employed in fields including flexible electronics, soft robotics and regenerative medicine. Currently, however, such hydrogels are often soft and fragile, limiting their practical utility. Researchers at Zhejiang University in China have now fabricated 3D-printed hydrogels that can be easily, and repeatably, switched between soft and hard states, enabling novel applications such as smart medical bandages or information encryption.
“Our primary motivation was to overcome the inherent limitations of 3D-printed hydrogels, particularly their soft, weak and fragile mechanical properties, to broaden their application potential,” says co-senior author Yong He.
The research team created the hard/soft switchable composite by infusing supersaturated salt solution (sodium acetate, NAAC) into 3D-printed polyacrylamide (PAAM)-based hydrogel structures. The hardness switching is enabled by the liquid/solid transition of the salt solution within the hydrogel.
Initially, the salt molecules are arranged randomly within the hydrogel and the PAAM/NAAC composite is soft and flexible. The energy barrier separating the soft and hard states prevents spontaneous crystallization, but can be overcome by artificially seeding a crystal nucleus (via exposure to a salt crystal or contact with a sharp object). This seed promotes a phase transition to a hard state, with numerous rigid, rod-like nanoscale crystals forming within the hydrogel matrix.
Superior mechanical parameters
The researchers created a series of PAAM/NAAC structures, using projection-based 3D printing to print hydrogel shapes and then soaking them in NAAC solution. Upon seeding, the structures rapidly transformed from transparent to opaque as the crystallization spread through the sample at speeds of up to 4.5 mm/s.
The crystallization dramatically changed the material’s mechanical performance. For example, a soft cylinder of PAAM/1.5NAAC (containing 150 wt% salt) could be easily compressed by hand, returning to its original shape after release. After crystallization, four 9x9x12 mm cylinders could support an adult’s weight without deforming.
For this composite, just 1 min of crystallization dramatically increased the compression Young’s modulus compared with the soft state. And after 24 h, the Young’s modulus grew from 110 kPa to 871.88 MPa. Importantly, the hydrogel could be easily returned to its soft state by heating and then cooling, a process that could be repeated many times.
The team also performed Shore hardness testing on various composites, observing that hardness values increased with increasing NAAC concentration. In PAAM/1.7NAAC composites (170 wt% salt), the Shore D value reached 86.5, comparable to that of hard plastic materials.
The hydrogel’s crosslinking density also impacted its mechanical performance. For PAAM/1.5NAAC composites, increasing the mass percentage of polymer crosslinker from 0.02 to 0.16 wt% increased the compression Young’s modulus to 1.2 GPa and the compression strength to 81.7 MPa. The team note that these parameters far exceed those of any existing 3D-printed hydrogels.
Smart plaster cast
He and colleagues demonstrated how the hard/soft switching and robust mechanical properties of PAAM/NAAC can create medical fixation devices, such as a smart plaster cast. The idea here is that the soft hydrogel can be moulded around the injured bone, and then rapidly frozen in shape by crystallization to support the injury and promote healing.
The researchers tested the smart plaster cast on an injured forearm. After applying a layer of soft cotton padding, they carefully wrapped around layers of the smart plaster bandage (packed within a polyethylene film to prevent accidental seeding). The flexible hydrogel could be conformed to the curved surface of limbs and then induced to crystallize.

After just 10 min of crystallization, the smart plaster cast reached a yield strength of 8.7 MPa, rapidly providing support for the injured arm. In comparison, a traditional plaster cast (as currently used to treat bone fractures) took about 24 h to fully harden, reaching a maximum yield strength of 3.9 MPa
To determine the safety of the exothermic crystallization process, the team monitored temperature changes in the plaster cast nearest to the skin. The temperature peaked at 41.5 °C after 25 min of crystallization, below the ISO-recommended maximum safe temperature of 50 °C.
The researchers suggest that the ease of use, portability and fast response of the smart plaster cast could provide a simple and effective solution for emergency and first aid situations. Another benefit is that, in contrast to traditional plaster casts that obstruct X-rays and hinder imaging, X-rays easily penetrate through the smart plaster cast to enable high-quality imaging during the healing process.
While the composites exhibit high strength and Young’s modulus, they are not as tough as ideally desired. “For example, the elongation at break was less than 10% in tensile testing for the PAAM/1.5NAAC and PAAM/1.7NAAC samples, highlighting the challenge of balancing toughness with strength and modulus,” He tells Physics World. “Therefore, our current research focuses on enhancing the toughness of these composite materials without compromising their modulus, with the goal of developing strong, tough and mechanically switchable materials.”
The hydrogel is described in the International Journal of Extreme Manufacturing.
The post Hydrogels rapidly switch from soft to hard to create smart medical bandage appeared first on Physics World.