Magnetically controlled microbots are small enough to diffract visible light
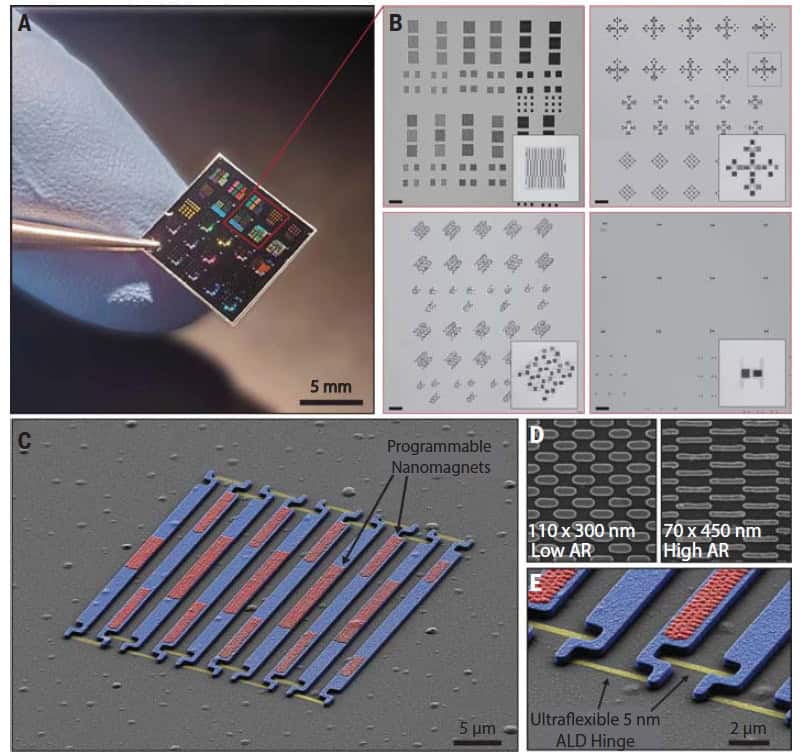
Microscopic robots with small-scale features that can control light at the microscale offer the potential to probe the microscopic world in more detail – with the scattering of light from such microbots able to induce diffractive optical effects.
To date, this combination of diffractive optics and tuneable mechanics has primarily exploited microelectromechanical systems (MEMS) devices, but creating actuatable microbots with features on the scale of the wavelength of light has been challenging.
To address this challenge, researchers at Cornell University turned to magnetically controlled microbots. While such robots have been developed at millimetre scales, the ability to perform magnetic actuation at the micron scale only became possible recently, due to the creation of protocols that encode magnetic information into microscale robotics and the use of atomic layer deposition (ALD) to create nanoscale hinges that make flexible micromachines capable of advanced navigation.
The team has now created magnetically controlled microbots that operate at the visible-light diffraction limit, so-called diffractive robots.
“A walking robot that’s small enough to interact with and shape light effectively takes a microscope’s lens and puts it directly into the microworld,” says team leader Paul McEuen in a press statement. “It can perform up-close imaging in ways that a regular microscope never could.”
New magnetic microbots
Using nanometre-scale mechanical membranes, rigid panels, programmable nanomagnets and diffractive optical elements, McEuen and colleagues created untethered microbots that are small enough to diffract visible light. They used the ALD hinges to connect the microbot’s rigid panels with magnetically actuatable joints, enabling them to reconfigure and move in millitesla-scale magnetic fields.
The core elements of the diffractive microbots comprise the light-diffracting panels with integrated nanomagnet arrays and the flexible hinges; the platform can also embed optical elements such as an optical diffraction grating. To enable the required mechanical, diffractive and magnetic performance, these integrated elements span several orders of magnitude in terms of their individual scales. The light diffracting grating panels were tens of microns in size, with each panel 1 µm wide, whereas the diffractive grating lines were on the scale of light wavelengths, the hinges had a thickness of 5 nm, and the magnetic domains were in the nanoscale realm.
The hinges played a crucial role, the researchers note, by providing a high degree of flexibility to an otherwise rigid robot. This flexibility allowed the microbots to rotate and reorientate themselves to dynamically change how light is diffracted, focused and redirected.
When manipulated with a magnetic field, the microrobots were able to simultaneously change shape, locomote along a surface and control diffracted light. This locomotion capability was due to the array of nanomagnets integrated into the light-diffracting grating panels.
By selectively controlling the aspect ratio of the nanomagnet domains and programming them using the strength of the external magnetic field, the researchers could control the movement of the microbots – including crawling forward on a solid surface and “swimming” through fluids while simultaneously steering and diffracting light.
“These robots are 5 microns to 2 microns,” says co-author Itai Cohen. “They’re tiny. And we can get them to do whatever we want by controlling the magnetic fields driving their motions.”
The researchers note that the tuneability of the optical elements could be further improved by adding more magnetic material to the microbots and/or increasing the size of the magnetic fields used to control them. And while this study centred around individual microbots, it should also be possible to use multiple microbots in magnetically actuated robot swarms to introduce collective optical effects.
Potential applications
As a generalized robotics platform, the microbots could easily be modified and produced with differing sizes, geometries and optical elements according to the intended application. Some key optical elements that could be integrated include meta-atoms, subwavelength apertures and plasmonic resonant probes.
The researchers have already demonstrated that the microbots have capabilities including force sensing with piconewton sensitivity, subdiffractive imaging using a type of structured illumination microscopy, and light beam steering and focusing using tunable diffractive optical elements. Other potential applications include endoscopic imaging and tissue ablation, high-resolution fluorescence microscopy of cells, and the high-resolution sensing of magnetic fields and current in integrated circuits.
The research is described in Science.
The post Magnetically controlled microbots are small enough to diffract visible light appeared first on Physics World.